Our SolutionsÂ
Accounting software that allows you to manage your entire business on the go.
Procurement Management System
Stay ahead with purchasing strategies that help keep your business lean and agile to meet the demands of the market.
Supply Chain Management
Know your real-time stock availabilities and movements. From single items to multiple warehouses, we have your supply chain covered.
Don't let your inventory dictate your business, command the flow of goods.
Sales Management System
Have a complete solution for sales that is flexible in a world of negotiations, discounts & credits.
Warehouse Management System
Knowledge is power, track exactly how your business is performing and where your funds are going with powerful real-time reporting.
Remove the hassle of creating reports from scratch. Use the out of the box reports that can give you the details you need to make a decision.
Accounting Management System
Know the value of your company. From purchasing and selling the fixed asset to having multiple depreciation books as well as disposal, you are able to see the changes in value of what you own.
Manufacturing and Production
Keep your processes lean while managing the fine detail by accounting for multiple levels of Bill of Materials and the use of items and resources.
Procurement Management System
Procurement Management System is a vital business process, wherein it mainly focuses on acquiring and receiving of items from the vendors/suppliers. It creates an impact to the overall costs, inventory, and assets of the company. It means that you do not submit it to a vendor. We help you develop your purchasing capabilities to the items from your suppliers to your inventory. We help you create purchase requisitions with just a few clicks.
​
We improve your purchase and inventory performance with procurement management system. Select from different replenishment methods for each product depending on your manufacturing and delivery strategies. Our procurement management system easily imports suppliers' price lists to make smarter purchase decisions based on promotions, quantities and conditions. Keep track of a product's availability from your supplier’s stock and check your order status for you to base your sales price from your supplier's prices.
​
Generally refers to the final act of purchasing but it can also include the procurement process overall which can be critically important for companies leading up to their final purchasing decision. Companies can be on both sides of the procurement process as buyers or sellers. Through this, we mainly focus on the side of the company.
Best Practices in the Procure-to-Pay Process

The following five best practices can help organizations improve the efficiency
and effectiveness of their procure-to-pay process:
​
-
Implement procure-to-pay process
-
Keep the process transparent
-
Improve supplier agreement
-
Optimize inventory
-
Streamline contract management
Benefits

Transparent Purchase Requisition
Accessible, complete and transparent purchase requests.

Flexible Processing
​
Customize every aspect of your Purchase Orders from data fields to approval workflows

Fewer Human Errors
​
Reduces the risk of purchasing issues from inappropriate data input

Workflow Automation
​
Simplifies activities related to purchase requisition, canvassing, purchase order, and goods receipt.
Sub-modules
Procurement Management System includes:
-
Purchase Requisition
-
Canvassing
-
Purchase Order
-
Receiving Report
Purchase Requisition
​
All requested items that are managed through purchase requisition. It can be set up in the system which are vendors that will be used for the requesting items. Most of the transactions are recorded in submodules and they are reconciled with the purchase orders in real-time. Transactions that can be done directly in purchase requisition include warehouse which are posted to select the delivery location of the item requested. The main objective of this module is for the enterprise not to order material in excess of requirement and as such could be helped by our Supply Chain Management Module. The Purchase Requisition form allows the Purchasing department to input the item the quantity and estimated unit cost of the item to be procured until the designated approver approves the Purchase Requisition in which he/ she may see the department and designated warehouse and the person who requested it.
​
The purpose of Requisition includes the following:
-
Increase speed. Requisitions can be processed and transmitted electronically across company; saving many days in routing through company mail. It also does not require you to send a runner or staff around to collect signatures. Requisitions used to take hours or days before can now be routed in minutes and faxed to the vendor from the Purchasing server, cutting down processing time tremendously.
-
Accuracy of funds. Requisitions route to the person(s) designated as the approver(s) for any fund(s) that are on a requisition. This allows departments to review the use of their funds before the order is created.
-
Ability to track the requisition at all points in the process. Departments can access the requisition at all times and see who has the order and what approvals or actions it is waiting on.
​
Canvassing
​
Canvassing primarily features the Request for Quotation (RFQ). RFQ allows you to issue a request to your vendor for a quote on a specific item or service. The Quotation is the official response from your vendor. The system will also propose the most favorable quote based on your entries from the Quotations (Lowest Bidder).
An RFQ typically involves more than the price per item. Information like payment terms, quality level per item or contract length are possible to be requested during the bidding process. An RFQ can have an approval process or release procedure if your company requires approvals before you send RFQ to vendors for bidding.
Purchase Order
​
Purchase Order is a sub module that captures all transactions with vendors and manages payment plans. Delivery dates and payment terms will be set and when transactions are posted in purchase order, then requisition will be updated with the items in real time. Transactions in purchase order include payment terms, delivery date, VAT, currency, and warehouse. The purchase order provides a comprehensive and fully integrated purchasing system. It allows combination of multiple receipts on a single invoice. The shippable backorder report helps identity orders that can be completed based on recent inventory receipt. It produces produce purchase orders for both products and services. It automatically creates an inventory system or choose to manually set up.
​
The purpose of Purchase Order Module includes the following:
-
Match Goods delivered against what was ordered. The team or individual that receives goods into stock when shipments arrive may well not be the same person that placed the order. If you’re only placing orders on the phone and not using Purchase Orders, then nobody really knows what you asked for.
-
See purchasing history with suppliers. Using Purchase Orders gives you a trail of invaluable information about your purchasing and cost cycles. Next time you have a meeting with a supplier to negotiate a discount or place a purchase order for the next season’s goods, you can go armed with the knowledge of exactly what you bought last year, what lines sold well, what you paid for them and how fast the supplier managed to deliver to you.
Receiving Report
​
Receiving Report is a sub module that captures all transactions with vendors and manages invoices. Item serials will be set and when items are received and transactions are posted in receiving report, then requisition will be updated with the items in real time. Transactions in purchase order include purchase order, invoice, supplier delivery receipt, and item serial. It is the physical inbound movement of goods or materials into the warehouse. It is a goods movement that is used to post goods received from external vendors or from in-plant production. All receiving reports result in an increase of stock in the warehouse.
Procure-to-Pay Process Flow
Coordinated and integrated action taken to fulfill a requirement for goods or services in a timely manner at a reasonable price. It involves a number a sequential stages, ranging from need identification to invoice approval and vendor payment. Steps in a procure-to-pay cycle need to be executed in a strict order.

Sales Management System
Sales Management System is a continuous and repetitive processes for selling goods (units, and even parts) to the customers. An efficient sales cycle could improve customer relationship and increase sales. It creates an impact to the customer orders, invoices, and sales of the company. Showing transactions settled at any given month, calculating discounts across a range of products, viewing sequence of invoices, credits entered in the transactions and processing collection applied to specific invoice.
We help you develop your sales capabilities to the customers and maintain customer orders. We help you create sales orders with just a few clicks. Gives the user's information and options on inventory location. We improve your sales and invoice performance with sales management system. Keep track of a product's availability from your inventory and check your customer order's status.

Benefits




Transparent Sales Order
​
Accessible, complete and transparent customer orders.
Flexible Processing
​
Customize every aspect of your orders from data fields to approval workflows
Fewer Human Errors
​
Reduces the risk of sales issues from inappropriate data input
Workflow Automation
​
Simplifies activities related to sales order, credit limit, delivery, and sales invoice.
Sub-modules
Sales Order
​
All requested items that are managed through purchase requisition. It can be set up in the system which are vendors that will be used for the requesting items. Most of the transactions are recorded in submodules and they are reconciled with the purchase orders in real-time. Transactions that can be done directly in purchase requisition include warehouse which are posted to select the delivery location of the item requested.
​
Sales Invoice
​
Purchase Order is a sub module that captures all transactions with vendors and manages payment plans. Delivery dates and payment terms will be set and when transactions are posted in purchase order, then requisition will be updated with the items in real time. Transactions in purchase order include payment terms, delivery date, VAT, currency, and warehouse.
Accounting Management System
Accounting Management System provides real-time fiscal information anywhere and on any device. When needed, we make it easy to communicate financial information to external partners. Our flexible accounting and finance tools can gather data and generate reports—which improves insight, automation, and compliance within your organization. We help you develop expansive functionality that supports multiple locations, currencies, companies, and tax codes. We empower managers by streamlining business intelligence so they can achieve optimal fiscal performance.
​
Fundamentally different from other computer-based and cloud-based accounting systems, It goes beyond basic accounting by providing reports and ready-to-use analytics and dashboard. The simple and precise transaction screen helps in optimizing the business process.

Benefits

Freedom from Duplicate Data Entries
​
Removes the process of tallying information between separate systems

In-depth Insights from Real-time Data
​
Provides you with in-depth visibility into the fiscal health of your organization.

Financial Information Transparency
​
Accessible, complete, and accurate monetary information

Robust Reporting Capabilities
​
Includes built-in and customizable filters that can be applied as needed for quickly generating accurate financial reports

Fewer Human Errors
​
Reduces the risk of accounting issues from inappropriate data input

Financial Data Security
​
Provides multi-layer security to the stored information and provides role-based access to authorized users to prevent security breaches

Workflow Automation
​
Simplifies activities related to accounts payable and accounts receivable, removes cash flow issues, and improves cash management

Manage All Your Accounting and Financial Needs
​
An efficient way to manage financial information, monitor costs, measure revenues, and oversee other aspects of your accounting process
Sub-modules
Accounting Management System includes:
-
general Ledger Accounting
-
Accounts Receivable
-
Accounts Payable
-
Asset Accounting
-
Bank Accounting
General Ledger Accounting​
​
All general ledger accounts that are used for reporting are managed through general ledger accounting. Chart of Accounts can be set up in the system which are accounts that will be used for the preparation of financial statements. Most of the transactions are recorded in submodules and they are reconciled with the general ledgers in real-time. Transactions that can be done directly in General Ledger Accounting include journal vouchers which are posted to adjust or correct transactions. Reversals can also be done from general ledger accounting. Balances in general ledger accounts can be displayed and trial balances extracted from the system.
Accounts Receivables​
​
Accounts receivables is a sub module that captures all transactions with customers and manages customer accounts. Separate customer accounts will be maintained and when transactions are posted in customer accounts, reconciliation accounts in general ledger are updated with the figures in real time. Transactions in accounts receivables include invoice posting, credit memo posting, down payments, invoice payment, dunning and executing customer reports.
​
Accounts receivable allows your business to manage all of the funds customers owe them. It will track customer payments as well as manage invoices and cash.
Accounts Payable​
​
Accounts payables is a sub module that captures all transactions with vendors and manages vendor accounts. Separate vendor accounts are maintained and when transactions are posted in customer accounts, reconciliation accounts in general ledger are updated with the figures in real time. Transactions in accounts payables include invoice posting, credit memo posting, down payments, invoice payment, automatic payment program and executing vendor reports.
​
Accounts payable will manage all of the funds your company owes to your vendors and other creditors. An accounts payable feature integrates your payable data with your purchasing system so you can take control of your cash flows. Automating accounts payable will save you money and time on labor hours as well as avoid human errors.
Asset Accounting​
​
Asset accounting manages all transactions related to assets for an entity. When transactions are posted in asset accounts, reconciliation accounts in general ledger are updated in real time. Transactions in asset accounting include asset acquisition, asset retirement, asset sale, asset transfer, asset revaluation and asset depreciation.
​
Asset management gives your organization better visibility in terms of utilization, costs and maintenance. For example, keeping track of the depreciation of your assets can help you forecast expenditures and create budgets. If you are aware that your equipment is aging and may need maintenance soon, you can plan accordingly for those payments.
Bank Accounting​
​
Bank accounting captures all transactions with the banks. Bank reconciliation is done to reconcile all transactions recorded on bank statements comparing them to transactions in the system.
Supply Chain Management
It is a full suite of enterprise application capabilities—including purchase management, sourcing, and procurement, inventory management, advanced material management, shipping and receiving, and warehouse management—and is complemented by forecasting, order management, and analytics capabilities. Combined, you have the solution you need to meet—and even exceed—customer expectations in today’s increasingly global marketplace.
​
A highly effective supply chain is critical to the success of your strategic growth initiatives. Top-performing manufacturers are empowering supply chain processes with innovative technology that is best fit for unique operational needs, easy to use, and informed by industry best practices. Drive out costs, increase velocity, and enhance your customer experience with a strong supply chain that is ready for the future.
​
It provides effective coordination from initial raw materials to the ultimate delivery of the finished product, transforming your supply chain into a results-driven value chain.
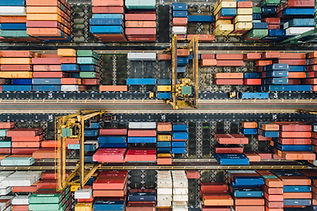
Warehouse Management System
Overview
The Warehouse Management System (WMS) leverages ERP, mobile ID data collection, and wireless communications to seamlessly link your warehouse with your order processing and manufacturing operations—optimizing your pick, pack, ship, and receiving processes.
Functionality includes:
-
Bin management
-
Warehouse team creation
-
Fulfillment workbench
-
Allocation template
-
Wave picking
-
Cross-dock tracking
-
Paperless picking
-
Queue management
Supply Chain Management Module Outline:​
-
Multi-site Management
-
Functionalities
-
Forecasting and Master Production Scheduling
-
Material Requirements Planning
-
Forecast Pro
-
Mobile Warehouse

Multi-site Management
​
Not only are manufacturers and distributors looking for new tools to oversee multi-plant operations, but they’re also looking to maximize the use of existing resources. Alternative production methods management helps optimize the production processes for specific parts in each plant, based on the resources available. Another optimization tool includes the transfer of material or semi-finished components to another plant for completion.
-
Material management – Provides core warehousing functions allowing users to initiate adjustments and movements from the warehouse floor. Offers an increased efficiency with cycle counts and stock takes. Enables efficient entry with automated workflows triggered by scan events.
-
Shipping – Scan pick validation option included. Process outbound shipments direct from the device. Functions include creating Master Packs and standard Pick Lists for customers not licensed for Advanced Material Management (AMM).
Functionalities
-
Receiving – Provides complete functionality to process an inbound container or purchase order, as well as intercompany and transfer order receipts. It provides users with effective and efficient serial and lot processing and multiple UOM scanning. Users can search for all open PO’s for a part by scanning parts barcodes.​
-
Trackers – Trackers help the shop/warehouse users in completing their daily routine.​
-
Material queue – Users can efficiently pick items assigned to their queue, grab items from the available queue, or return items back to the queue. Users can select an outbound order and select all material queue transactions related to the order, to the users’ queue. Advanced sort and filter functionality allows users to save to a named query and dynamically add to the sub-menu. Unpicking sales or transfer orders functionality is also included.
Available as an extension to Scheduling, the Advanced Planning and Scheduling incorporates the strength of the Scheduling engine and enhances it with advanced functionality such as multiple constraint scheduling, a wide range of scheduling methods, visual drag-and-drop scheduling, capability and dependent capability-based scheduling, real-time capable-to-promise functionality, and advanced material planning functionality.
​
​
-
Minimum WIP Scheduling – Use a unique scheduling algorithm designed to minimize work in the process by scheduling a job to ship as early as possible. APS then back schedules to start working on the job as late as possible.
-
Dimensional Planning – Schedule by volume and quantity using dimensional planning that is not time-constrained.
-
Rate-Based Scheduling – Schedule cells based on production throughput rates rather than time.
-
Material Constraints – Consider material availability as a scheduling constraint. Integrated directly with Inventory and Purchasing, the APS system knows when the material is due and schedules accordingly.
-
Advanced Material Planning – Increase throughput by considering material and component availability as a constraint. Advanced material planning, an integral feature of APS, facilitates intelligent stocking and procurement of material requirements. The schedule function recognizes materials earmarked as constraints, gives the master scheduler material availability, and considers supplier calendars for a more realistic schedule.
-
Change Impact Analysis – See the immediate impact of proposed changes on other orders to make informed decisions about desired changes.
-
Time Adjustment – Automatically take into account resource utilization and resource group efficiency for more accurate load calculation.
-
Optimization Rules – Generate a schedule based on rules assigned to individual resources.
-
Balanced Optimization – Concurrently consider a priority, slack time, and setup time when determining load balance.
-
Single Cell Scheduling – Schedule an entire job or assembly within a single work cell.
-
Unlimited What-If – Create unlimited what-if scenarios to view the effect of changes on your shop floor.
-
Multi-Plant Communication – Help to ensure that interdependent plant schedules are coordinated.
Planning and Scheduling
Performance-driven companies have mastered the art of predicting and responding quickly to changes in customer demand with a minimal business interruption. Whether you are a global, multisite enterprise or a single site manufacturer or distributor, precise and flexible planning and scheduling are imperative to efficient and profitable operation. Offering a comprehensive solution for forecasting, material requirements planning (MRP), scheduling, and advanced planning and scheduling to meet the needs of today’s agile business.
​
The Advanced Planning and Scheduling includes:
​
-
Capable-to-Promise – Easily manage customer expectations with real-time capable-to-promise functionality in Order Management. It is capable of to-promise uses the scheduling engine to determine accurate promise dates and offers order processing single-click confirmation or order cancellation based on the projected due date.
-
Multiple Resource Scheduling Board – Easily manipulate the schedule with drag-and-drop manipulation and drill-down techniques for multilevel assemblies and operation details. The main control center for scheduling resources graphically displays schedules for a group of resources on one screen. Dynamically change the timeline of the view to see minute operations and quickly analyze the impact of long-running operations. Add memos to a schedule on the Multi-Resource Scheduling Board about any aspect of a current schedule.
-
Multiple Constraints – Set up every operation with multiple constraints or resources (e.g., machines, tools, skilled labor, raw materials, or available subassemblies)
-
Resource Eligibility – Define resources within a specific resource group with individual characteristics to improve scheduling accuracy.
-
Automated Scheduling by Capability– Define a capability or skill level that can be tied to multiple resources rather than a resource group or individual resource in the planning process. The APS engine then determines, based on the available resources, which individual resource to schedule for the operation.
-
Dependent Capabilities – Link-dependent capabilities that the scheduling engine schedules along with the primary capability when operations require dependent skills to perform the operation.
-
Finite or Infinite Capacity – Define each resource with either finite or infinite capacity. When a piece of the schedule is moved, the resource is rescheduled according to its type.
Material Requirements Planning
​
Built for the needs of a single site as a well as extended enterprise, MRP offers cross-plant and cross-company planning. Enhanced to offer plant source as well as product group sourcing of materials and assemblies, MRP automatically and visually extends the enterprise to efficiently manage supply and demand, from forecasting and MPS to MRP generation, and more. Material Requirements Planning functionality includes:
​
-
Sourcing By Plant – Define a unique source per part or plant— whether its default sourcing is purchased, produced, or transferred. What is produced in one location may be purchased—or transferred in—from another.
-
Available-to-Promise – View running balances with the available-to-promise function. Enter a quantity, and the system will find the earliest date that quantity will be available. Enter a date, and see how many parts are available on that day. MPS, forecast, order, and planned receipt quantities are visible to help you in your production planning tasks.
-
Planning Types – Maximize your planning accuracy with multiple types of inventory planning, including minimum/maximum/multiple, days of supply, and run out.
-
Rough Cut Horizon – Enable MRP to process more efficiently by removing the time spent scheduling beyond a specified threshold or rough-cut horizon.
-
Recycle Jobs – MRP reuses un-firm jobs for optimum MRP performance.
-
Short Horizon Days of Supply – To optimize MRP performance, a Short Horizon Days of Supply field is included within the Part Maintenance program on the Plant Detail sheet. This field defines a material value that will be used when MRP determines that the needed materials fall within the Short Horizon.
-
Calculate Manufacturing Lead Time – Plan for part components lower down in the assembly structure for accurate MRP scheduling.
-
Start Minimum Quantity – Account for partial material availability in MRP calculations to get started earlier with available material and improve delivery performance.
-
Bill of Materials Check – MRP checks the revision level and verifies approvals before pulling in a standard BOM and routing. For parts that do not have a current approved revision, a job suggestion is created in the new/change order queue to help ensure requirements are not lost.
Demand Planner
​
Demand Planner provides cloud-based statistical forecasting that automatically selects the right forecast model for each item—accounting for trend, seasonality, and promotion/event-driven demand. For companies that manage many items like component parts, service parts, material requirements planning, or high-tech equipment, it includes an intermittent demand model so you can accurately forecast the inventory needed to hit desired service levels.
Forecast Pro
​
Forecast Pro is designed to support large-scale forecasting jobs, collaborative forecasting, working with complex hierarchies, maintaining multiple forecasts overrides, documenting your forecasting sessions, and integrating with historical data from your ERP and other systems. With Forecast Pro you can create accurate forecasts quickly and easily using proven statistical forecasting methods such as Exponential Smoothing, Box-Jenkins, Event Models, Multiple-level Models, Seasonal Simplification, Low Volume Models, Intermittent Demand Models, Moving Averages, Curve Fitting, and Simple Methods.
​
Handheld Support: Whether doing physical inventory or material moves or looking up serialized part information, the Handheld application offers an easy-to-use interface that is designed for plant and distribution employees. The Handheld module allows you to track your inventory as it moves throughout your enterprise with real-time data capture to improve inventory accuracy and speed up the order-to-ship cycle. Providing your users with event-based directing and routing of all managed tasks in real-time, the Handheld module not only helps you maintain complete transaction event history for analysis and reporting purposes but when coupled with Advanced Material Management, it also provides detailed tracking of material requirements and WIP information through mobile access to the material and picks orders queue. Complete functionality also includes:​
​
-
Auto-print-control support
-
Labeling support
-
Auto put away processing
​​Mobile Warehouse
Designed and fully integrated into the ERP, the Mobile Warehouse is the next generation of handheld applications for the warehouse environment. A modern and intuitive application, The mobile warehouse provides complex sort and filter options for users that include both part level and bin level validation. Scan validation is a configurable feature as well. Shortcuts to favorites and the frequently visited, as well as automated workflows triggered by scan event, improve the user experience. The Mobile Warehouse optimizes workflow for fast and accurate scanning, improves time to process transactions, increases accuracy, and reduces errors. It is compatible with the latest scanning devices running on Android® 5 or higher from Honeywell® and Zebra®. Simply download the application from the Google Play™ store into your device and start using it with minimal setup.
​
​
Once the baseline forecast is produced, it is available for collaborative review and consensus planning by authorized stakeholders. In addition, forecast accuracy can be measured to ensure the best possible forecast is delivered to the business at both the aggregate and item-mix levels. The Smart Demand Planner seamlessly integrates with the ERP software using an “out of the box” connector that simplifies implementation and support.
Manufacturing and Production
Streamline your entire manufacturing process from production planning and
scheduling, through sequencing and execution, to monitoring and analysis,
and improve efficiency along your entire value chain.
ERP is designed to ease manufacturing systems management.
Manufacturing and Production Module Outline:
​
-
Work Orders
-
Production Entry
-
Shop Control
-
Project Accounting
-
Shipping and Receiving

Work Orders
​
Work Orders is designed for manufacturing firms that require work order processing, component allocation, routing, and Material Requirement Planning (MRP) features. Work Orders can be automatically generated from sales order requirements, inventory shortages, or inventory forecast requirements. By defining work centers and operation steps, users can create flexible labor routes.
​
Production Entry
​
Production Entry is designed for companies that need a bill of materials, sales kit, configuration, or backflush processing, but don’t require the allocation of BOM components. It supports unlimited levels of bill materials and real-time costing from the Inventory Module. Modular and variable BOM types are available to handle product configuration issues with speed and flexibility, as well as maintaining fewer BOMs.
​
Shop Control
​
Shop Control provides shop floor capacity scheduling, what-if planning capabilities, and WIP tracking for production managers who require Manufacturing Resource Planning (MRPII). It imports open work orders with defined routes, identifies bottlenecks, and calculates work order completion dates. What-if plan orders can be created to view resource requirements without affecting real-time purchasing decisions.
​
Project Accounting
​
Project Accounting provides a budget and costing tool for project accounting and job cost management. Its design allows up to four levels of cost tracking with project, phases, category, and cost-type definition. The job account mask supports the optional use of phrases and/or categories, and cost-types are user-definable.
​
​​
Forecasting and Master Production Scheduling
Forecasting and Master Production Scheduling (MPS) is included with the Material Requirements Planning module and is designed to assist manufacturers and distributors with both day-to-day control and long-range planning and decision making. Forecasting and MPS support businesses that operate multiple, mixed-mode strategies simultaneously. Forecasting & Master Production Scheduling functionality includes:
​
-
Forecasting – Forecasts can be generated from multiple historical sources (e.g., sales, invoice, and inventory usage history). Users can also manually enter forecasts for companies, plants, customers, dates, and parts, cut-and-paste from other applications into the forecast system, or generate forecasts from multiple historical sources. Another option is to export and import forecasts to and from other applications or customers. Import options allow forecasts to be broken down by part, customer, plant, date, and company. This import can update the existing forecast, be a new forecast, or be completely clear and re-load.
-
Forecast Buckets – Bucket forecasts for variable periods: daily, weekly, monthly, yearly, etc.
-
Forecast Analysis – Forecast any number of variables (e.g., revenue) rather than just forecasting product units. Forecasting allows any number of tiers to be forecast and analyzed (e.g., forecasting product units by company, state, city, and customer).
-
Inter-Company – Trading Dynamically accepts forecasts from other companies within the enterprise. This allows companies to give visibility to the supply company of future demand without needing to raise a firm intercompany order.
-
Master Production Schedule – Enter production forecasts for specific end parts using the MPS function. Perform an iterative process of entering a planned schedule, viewing the effect on your resources, then modifying the plan until you have achieved an optimal schedule. Manually enter or cut-and-paste MPS from other applications or automatically generate the MPS from the forecast.
-
Driving Capacity and Raw Material Procurement – Make and alter MPS decisions based on constraints. Both forecasting and MPS can independently drive future demand.